Plastic panels are increasingly becoming the go-to choice for a wide range of commercial, agricultural, and industrial projects. Whether for roofing, siding, greenhouse construction, or interior cladding, their affordability, lightweight handling, durability, and visual appeal make them a resourceful solution across many sectors.
But as with any construction material, the performance of plastic panels is only as strong as their installation. Incorrect installation can lead to premature wear, water intrusion, cracking, or even structural compromise. For B2B professionals such as contractors, architects, suppliers, and project managers, knowing how to properly install and secure plastic panels is key to delivering long-lasting, high-quality results.
In this guide, we’ll explore the best practices, tools, materials, and techniques necessary to successfully install and secure plastic panels in a way that supports both functionality and longevity.
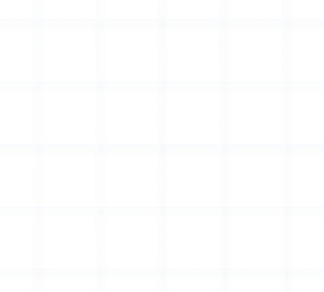
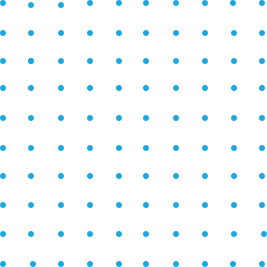
An Expert is just around the corner.
With over 100 years of combined product knowledge and industry experience, we are confident our plastics experts can help you find a solution for your application.
Choosing the Right Panels
The first step in a successful installation begins long before a screw is drilled; it starts with choosing the right type of panel for the job. Several universal materials are available, each with distinct properties and ideal use cases.
Polycarbonate panels are often favored for environments that demand high-impact resistance and excellent light transmission, such as greenhouses, skylights, and commercial roofing. Available in clear or tinted formats and in solid or multi-wall variations, polycarbonate is known for its strength and UV resistance.
PVC panels, by contrast, offer a highly economical and low-maintenance solution. They’re commonly used for siding, interior cladding, garages, agricultural structures, or temporary builds where cost-efficiency is a major factor. While less impact-resistant than polycarbonate, PVC still performs well in a wide variety of conditions.
Corrugated plastic panels provide a structural advantage in roofing systems thanks to their rigid design, which enhances load distribution and water drainage. They’re particularly valuable in outdoor structures where strong winds, rain, or snow loads are considerations.
Planning and Preparation
Before beginning installation, proper planning and site preparation are essential to ensure a secure, long-lasting result. Once you've chosen the right plastic panel for the project, assessing the installation area and materials is important to avoid preventable issues later. Pay close attention to framing compatibility, panel storage conditions, and handling guidelines.
Keep the following points in mind during the planning phase:
-
1. Confirm Support Structure
Make sure the support structure is properly engineered to accommodate the specific type of panel being installed.
-
2. Keep Panels Shaded & Dry
Prolonged exposure to direct sunlight may cause the UV protective film to bond to the panel surface, making it difficult to remove without damage.
-
3. Store Panels on a Flat Surface
Lay panels flat on a smooth, stable surface to prevent warping. Avoid sliding them over rough or sharp surfaces to protect against scratches and surface damage.
-
4. Confirm the Correct Side Faces Outward
Identify which side of the panel has UV protection by reading the printed film. This side must face outward during installation.
Installation Techniques
While attaching plastic panels may appear simple, the details in your installation method can make a major difference in both durability and performance. The approach you take will depend on the type of panel you're using and the material of the supporting structure, whether it's wood, metal, or aluminum. Each combination may require a specific fastening technique to ensure a secure and weather-resistant installation.
Key Installation Tips
Roof and Wall Fastening Guidelines
- Fasteners should always be placed on the ridges (high points) when working with corrugated panels on roofs. This minimizes the risk of water intrusion around the screw heads.
- For wall installations, fasteners are often applied in the valleys, depending on how the structure is exposed to the elements and the look you're trying to achieve.
Thermal Expansion and Contraction Guidelines
- Plastic panels naturally shift with temperature changes, so pre-drilling the holes slightly larger than the screw diameter (typically by 1.5mm to 2mm) is essential.
- Pre-drilling allows the panel to move without stress. Skipping this step can lead to cracks, fastener failure, or panels pulling away from the frame.
Recommended Fasteners
- For optimal results, use washer-head screws with neoprene or rubber gaskets. These help create a tight, watertight seal and evenly distribute pressure, which prevents damage at the fastening points.
- Several joining systems are available if your project involves joining panels side by side. A basic option is the polycarbonate H-profile, which slides between adjacent panels to hold them in place.
- Consider base and cap systems for greater strength and a more refined appearance. These two-piece joiners, available in polycarbonate and aluminum, start with a base secured to the frame.
- Once the panels are in position, the cap is either snapped or screwed into place, locking everything together securely.
Sealing and Weatherproofing
Effective sealing protects your structure from moisture, wind, and UV degradation. The internal channels must remain breathable for multi-wall polycarbonate panels to prevent condensation buildup. This is why vent tape is applied at the bottom of the panel and foil tape at the top. These specialized tapes help prevent dirt, insects, and moisture entry while allowing internal airflow.
End caps, made from polycarbonate or aluminum, help protect panel edges from weather exposure and should be applied over taped ends. Always use compatible, non-acidic sealants when securing caps or flashing. Applying too much silicone or using it to seal internal channels is a common mistake that can trap moisture and void panel warranties.
Panels used on sloped roofs should always overlap correctly, with the upper panel sitting over the lower one. A minimum roof pitch of 5–10% (around 1 inch per 10 inches of run) is necessary to ensure adequate water runoff and reduce the risk of leaks.
Working with Removable Panels
In certain commercial applications, plastic panels need to be removed and reinstalled often. This is common in industries like signage, marine, transit, or industrial design, where access panels, inspection hatches, or display elements are updated or serviced regularly. In these cases, choosing the right fastening system is especially important to guarantee long-term functionality and safety.
While plastic fasteners may appear to be a cost-effective solution initially, they tend to wear out quickly with repeated use. For high-use or high-traffic environments, more durable options are strongly recommended.
Consider the following fastening solutions for removable panel applications:
Best Fastening Solutions For Plastic Panels
- Stainless steel fasteners offer excellent durability and resist corrosion, heat, and wear, making them ideal for outdoor or marine environments.
- Z-clips provide strong vertical mounting support, functioning like a metal cleat, and are commonly used in signage and modular paneling.
- Fast-Con quick fastening systems allow secure, tool-free attachment and removal, ideal for applications requiring frequent access or updates.
- Metal fasteners generally maintain grip strength through hundreds of removal cycles without damaging the panel or mounting surface.
Avoiding Common Mistakes
Even experienced installers can face issues if a few basic guidelines are overlooked. One of the most common errors is installing multi-wall panels with the ribs running horizontally. This traps condensation, leading to mold and discoloration. Always run the ribs vertically to allow moisture to drain naturally.
Another mistake is over-tightening fasteners, which can cause stress fractures around the screw holes. Using the proper washer head fasteners and avoiding excessive torque can prevent this.
Trying to splice panels horizontally or skipping expansion gaps are also frequent issues. Always use full-length panels for the best results, and plan for temperature-related movement with proper spacing.
Keeping Panels Performing at Their Best
Once installed, plastic panels need very little maintenance, but regular inspections go a long way in extending their lifespan. Check fasteners and sealant joints twice a year, especially after storms or seasonal temperature shifts. If any sealant begins to degrade or separate, reapply to prevent water ingress.
Clean panels with a soft cloth or sponge and mild soap and water. Avoid using abrasives, harsh solvents, or high-pressure sprays that can damage the surface or strip away protective coatings.
Need Professional Insights?
For B2B professionals, installing plastic panels is more than a basic construction task; it’s an opportunity to deliver quality, reliability, and long-term value to your clients. With the right planning, tools, techniques, and ongoing maintenance practices, you can ensure every plastic panel project meets the highest standards.
Whether managing large greenhouse builds, retrofitting warehouse skylights, or outfitting agricultural sheds, following these best practices will help you avoid pitfalls, reduce callbacks, and enhance client satisfaction. If you’re looking for material recommendations, technical specs, or bulk-order solutions, we’re here to help.
Learn More
Our team can assist with selecting the right panel system for your project’s needs and provide ongoing support for installation and performance questions. Contact your local distributor now!
Get In Touch